Fogão para banho de cano: as sutilezas da fabricação
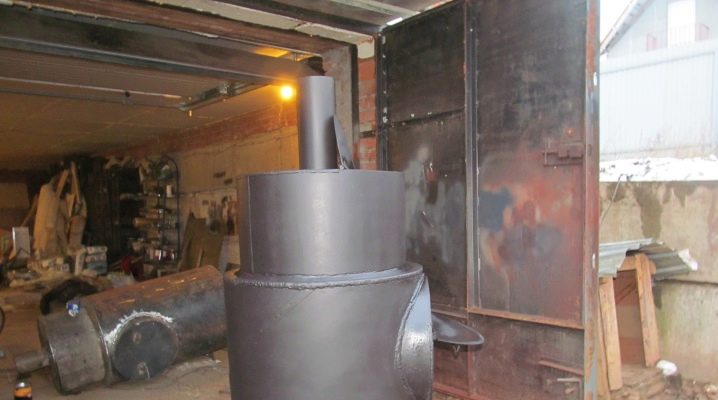
Entre os amantes da recreação ao ar livre ou adeptos de um estilo de vida saudável, dificilmente há alguém que não goste de tomar banho de vapor. Hoje, muitos residentes de verão se esforçam para adquirir suas próprias casas de banho. Recentemente, a criação independente de um fogão de sauna a partir de um cilindro ou tubo tem ganhado força. Construir um fogão de tijolos sólidos requer certas habilidades e habilidades, entre outras coisas, esse fogão ocupa mais espaço e você pode comprá-lo em uma loja de ferragens, mas custa uma certa quantia de dinheiro. Enquanto um forno de metal é uma opção mais econômica e é muito mais fácil de fazer você mesmo, sem mencionar o fato de que você pode confiar esse trabalho a um soldador.
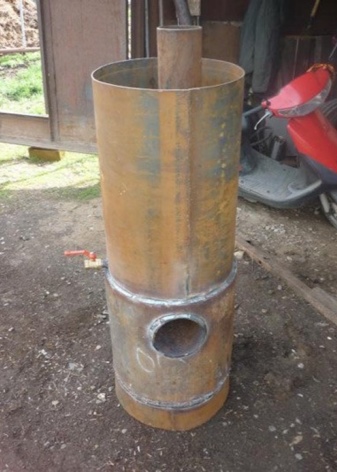
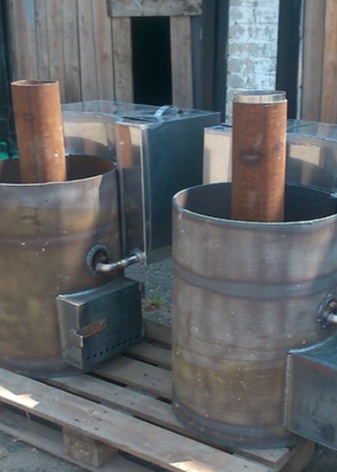
A estufa, fabricada de forma independente, respeitando os cuidados de segurança, não constitui uma ameaça para a vida e saúde humana, uma vez que o seu corpo estanque não emite monóxido de carbono durante o funcionamento.
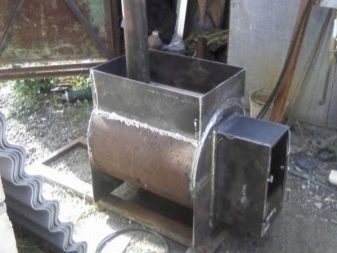

Características: prós e contras
O material de partida para um fogão de banho de metal pode ser não apenas um tubo ou um cilindro, mas também usa uma folha de aço.
As lâminas geralmente são constituídas por um corpo em forma de paralelepípedo retangular, porém, esta forma possui características próprias:
- as folhas devem primeiro ser cortadas, cortadas e unidas com uma máquina de solda;
- como resultado, esse forno custará mais;
- uma fornalha cilíndrica conduz melhor o calor;
- com base na trajetória de movimento dos gases de combustão, uma seção transversal circular é mais preferível;
- paredes planas são mais suscetíveis a queimar do que tubos feitos exatamente do mesmo material.
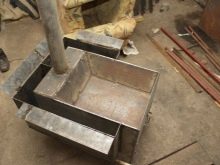
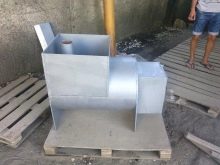
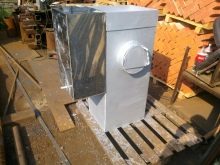
Quais são as vantagens dos fornos metálicos:
- o cilindro é apenas ligeiramente inferior à forma esférica em termos de condutividade térmica;
- a espessura das paredes das tubulações de água ou gás permite atingir altas taxas de condutividade térmica;
- o forno pode ser movido, é durável;
- o custo de fabricação de tal forno é muito baixo, uma vez que os cortes de tubos são freqüentemente vendidos a preços baixos;
- instruções de fabricação detalhadas indicando tamanhos e diâmetros de tubos irão reduzir a intensidade de trabalho do processo e economizar tempo;
- muitos produtos de fábrica deste tipo são feitos exactamente dos mesmos cachimbos, cuja imagem e semelhança é fácil recriar o produto artesanalmente;
- além disso, tais dispositivos são resistentes ao calor, à corrosão, duráveis e toleram facilmente temperaturas extremas.
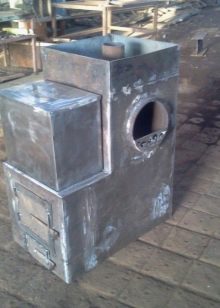
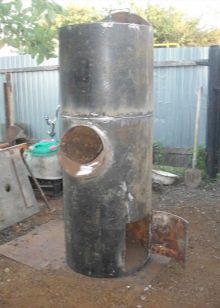
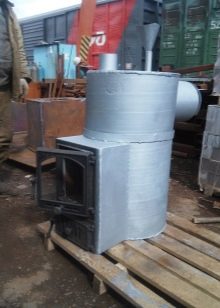
É claro que esses fornos têm suas desvantagens - o processamento de um tubo de metal espesso requer a aplicação de força física e ferramentas para um determinado tipo de trabalho.
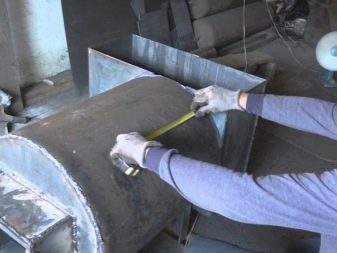
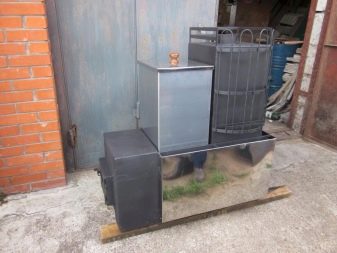
Tipos e características
Por localização no espaço, os fornos feitos de tubos são divididos nos seguintes tipos:
- vertical;
- horizontal.
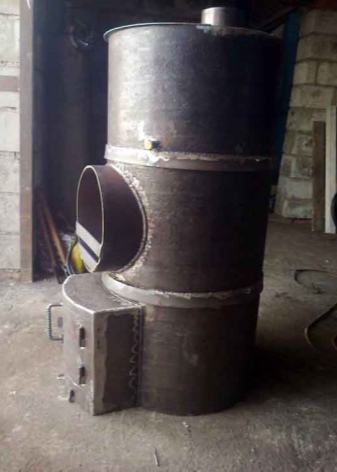
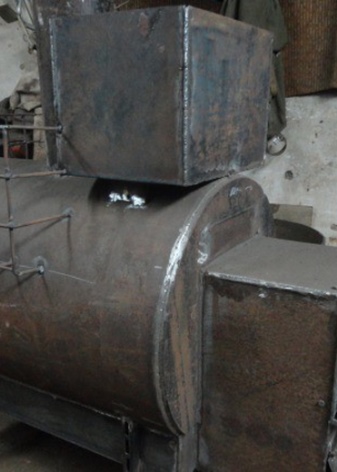
O fogão vertical se parece com um fogão de barril, mas tem diferenças - um recipiente adicional para pedras e um recipiente para água.
Forno caseiro vertical ocupa menos espaço, o que é de grande importância para as pequenas dimensões da sala de vapor, porém, pelo mesmo motivo, é inferior ao forno horizontal em termos de tempo de queima e intensidade de transferência de calor. No processo de combustão do combustível, o calor sobe, as paredes laterais não têm muito tempo para aquecer. Em uma fornalha horizontal, o processo é diferente - já que o ar aquecido no caminho para a chaminé aquece simultaneamente a abóbada do corpo. Com base nisso, fica claro que a eficiência de um forno horizontal será maior do que a de um vertical.A principal desvantagem desse projeto é a localização das portas do soprador e da fornalha diretamente na sala de vapor.
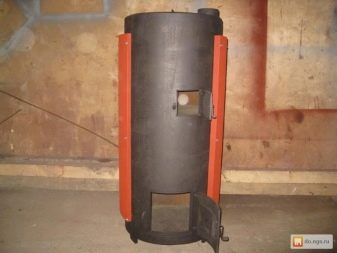
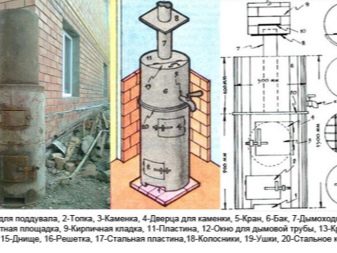
O combustível em um tubo vertical queimará mais rápido se a porta do cinzeiro não estiver fechada, interrompendo assim o acesso do oxigênio ao fogo. Em tal tubulação, o fogo interage de uma só vez com todo o volume de lenha, enquanto em uma tubulação horizontal o combustível é consumido gradativamente, o que é mais lógico para o aquecimento de um banho. Além disso, na forma horizontal do fogão, a cobertura das pedras de aquecimento é maior e a convecção do ar quente é maior, além disso, as portas do soprador e da fornalha, que estão localizadas bem na extremidade do tubo, o tornam possível retirá-los da sala de vapor. Tanto o primeiro como o segundo tipo podem ser feitos à mão.
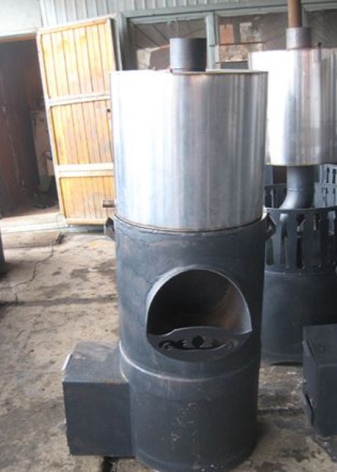
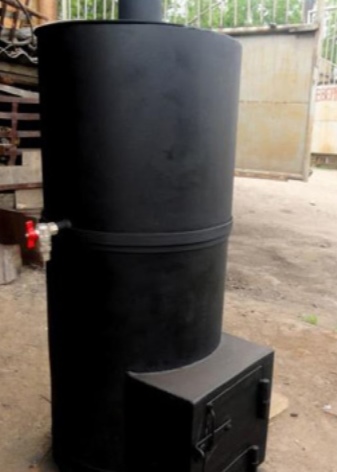
Preparação
É claro que um fogão feito à mão não terá um aspecto requintado ou originalidade, mas desempenha a sua função não pior do que um de fábrica e aquece perfeitamente um banho turco com uma área até 20 m2.
Em primeiro lugar, o tubo deve cumprir suas funções principais., ou seja, absorver e gerar calor uniformemente e ao mesmo tempo ter paredes suficientemente grossas para que o recuperador não tenha medo de altas temperaturas e dure muito tempo. Falando sobre as características básicas dos tubos, é necessário levar em consideração não só o diâmetro da seção transversal e a espessura da parede, mas também o tipo de aço. É claro que, ao usar recados, essas informações nem sempre estão disponíveis.
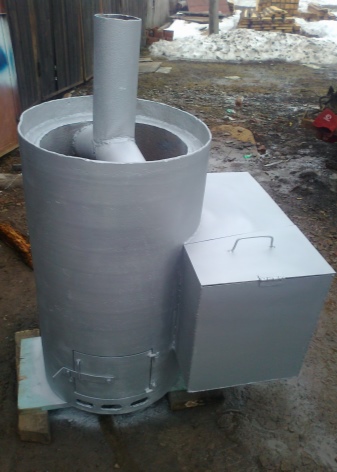
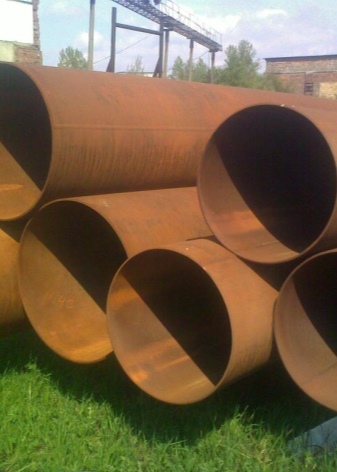
Falando sobre um banho padrão, os seguintes tamanhos são considerados ideais:
- diâmetro da seção - 0,5-0,55 m;
- espessura da parede - 8-12 mm.
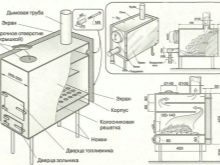
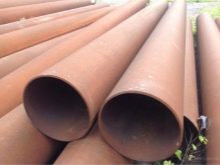
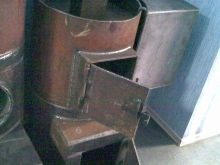
Ressalta-se que quanto maior o diâmetro, maior será o consumo de lenha.
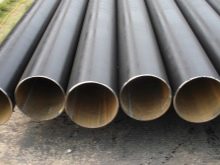
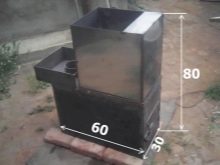
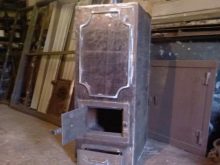
Preste muita atenção à qualidade do material: para a fabricação de um forno em banho, apenas tubos de aço são adequados, e não é necessário aço com alto teor de carbono. Não é adequado para trabalhos de perfil, porque as suas costuras podem facilmente perder a forma ou mesmo desfazer-se. O aço com alto teor de carbono pode ser identificado pelas faíscas que aparecem quando o metal e o anel de esmeril interagem - faíscas brancas se espalharão em todas as direções. O aço com baixo teor de carbono, por sua vez, produz faíscas de tonalidade amarelada, que apresentam trajetória retilínea, e as peças de aço inoxidável não funcionam. A melhor opção é o aço com um teor de carbono de cerca de 2%. Além disso, ao escolher um metal, é melhor evitar ligas de aço - também é fácil calcular usando uma máquina de esmeril: as faíscas da interação com o metal serão laranja, vermelhas ou brancas brilhantes.
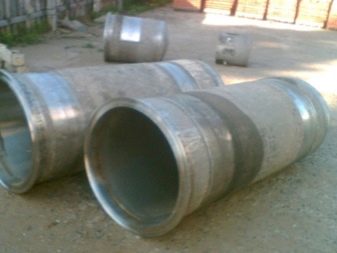
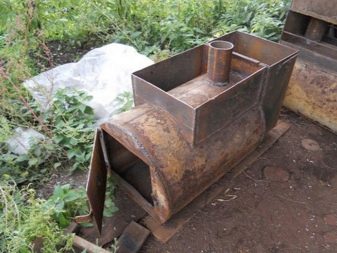
Em nenhum caso deve ser utilizado ferro fundido, pois se deteriora ao entrar em contato com a água.
Outras vantagens dos tubos de aço:
- resistência a danos mecânicos, alta transferência de calor e baixo coeficiente de expansão quando aquecido;
- preservação do calor mesmo após a combustão completa da lenha.
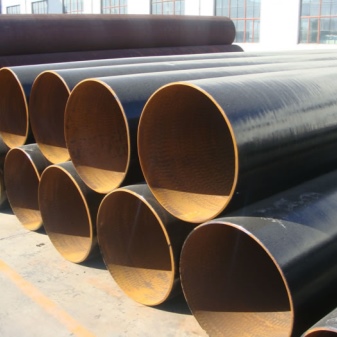
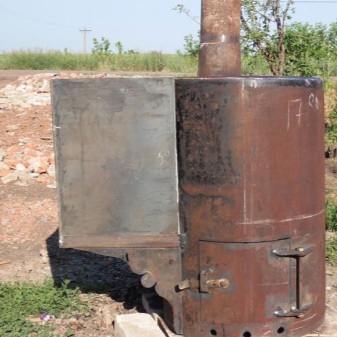
Os tubos possuem características próprias de acordo com a especificação. Vamos considerar essas informações com mais detalhes.
Os tubos redondos são classificados de acordo com o tamanho do seu diâmetro interno. O segundo número indica a espessura das paredes, os seguintes fornecem informações sobre o seu tipo e outras características. É comum considerar um milímetro como unidade de medida. Se os tubos são perfilados, os primeiros dois caracteres indicam o tamanho máximo da seção transversal, o terceiro número - a espessura da parede. As indicações "530 por 10" significam que o diâmetro do tubo ao longo da parede interna é de 530 mm, a espessura é de 10 mm, o diâmetro externo é de 550 mm com um erro de +/- 5 mm, levando em consideração a tolerância lateral, que é de 10%. A tolerância de taxa de fluxo predominantemente é aplicada à elipticidade.
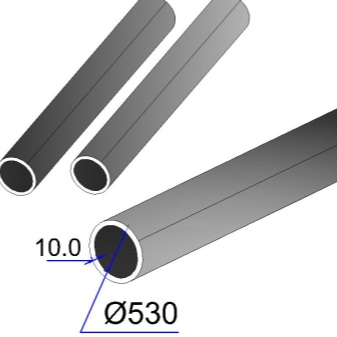
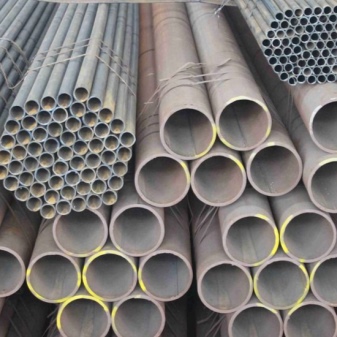
A espessura da parede do tubo também varia.
Os canos de água são divididos nas seguintes subespécies:
- leve;
- comum;
- fortificado.
De uma forma ou de outra, os tubos mais populares têm um diâmetro de seção transversal de 530 mm, sua espessura é de 6-12 mm e o valor nominal é de 6, 8 ou 10 mm.
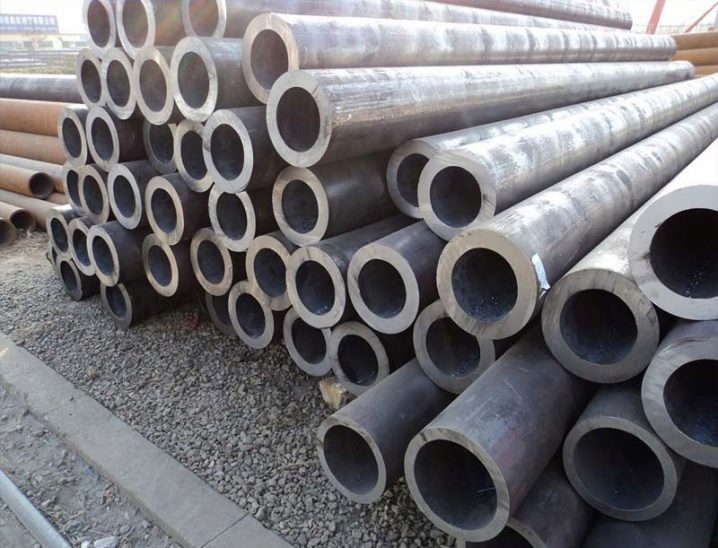
Esta informação é necessária para uma preparação imediata e correta dos materiais para o futuro recuperador.A melhor opção para um diâmetro de tubo é de 0,5 m, o que implica uma boa capacidade térmica e um trabalho confortável. Os tubos com valor nominal de 500 mm e mais têm um passo de 10 mm e são geralmente classificados como tubos de grande diâmetro. É muito mais fácil pegar imediatamente tubos que combinam entre si no diâmetro da seção transversal e espessura da parede, a fim de tornar mais fácil para você desenhar uma estrutura concêntrica e reduzir as lacunas entre eles.
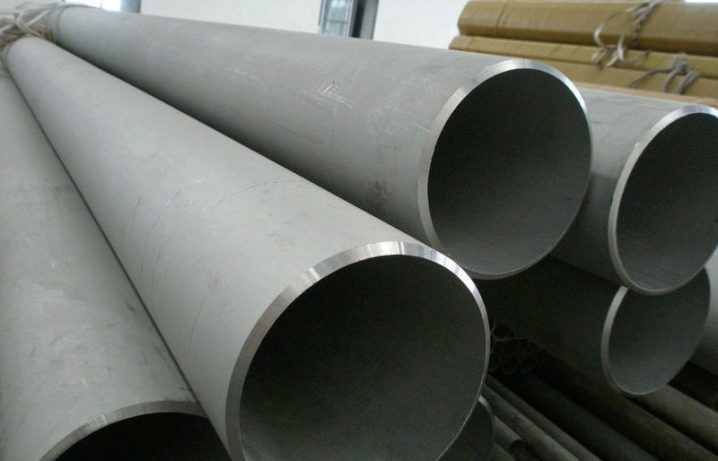
Os tubos são um dos produtos mais solicitados., portanto, não faz sentido regulá-los de maneira muito escrupulosa. Tubos que variam de 250 a 400 mm têm uma ampla faixa de seleção. Se possível, para a fabricação de um fogão para sauna, dê preferência a restos de tubos em espiral (sua designação é GOST 20295 85). Comparando-os com tubos soldados longitudinais (GOST 10704-91), eles têm valores de elipticidade mais baixos, são mais precisos e os vendem ao mesmo preço da sucata. Tubos fundidos maciços sem costuras são uma opção ainda melhor, mas só são adequados para fazer peças pequenas, pois seu diâmetro não ultrapassa 250 mm.
Ao se preparar para o trabalho, prepare um local de trabalho - pode ser uma garagem ou uma oficina em casa.
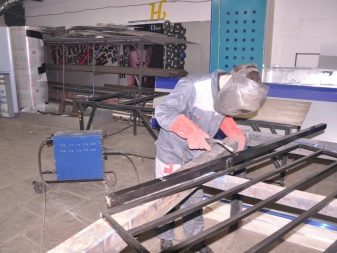
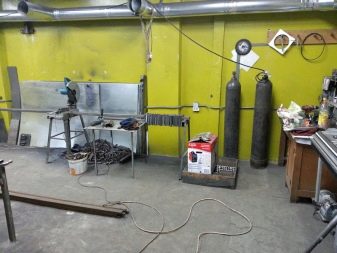
Materiais (editar)
Para a execução da obra, são necessários os seguintes materiais:
- o próprio tubo, que será necessário para criar uma fornalha e um tanque de água, seu diâmetro deve ser de 500 a 600 mm (530 mm é considerado o ideal), espessura da parede - de 8 a 16 mm, comprimento - de 1,2 a 1,5 m ;
- um cano que depois se tornará receptáculo de pedras - seu diâmetro é de cerca de 400 mm;
- chaminé - diâmetro 120-150 mm, espessura 2-4 mm;
- folhas de metal na quantidade de várias peças, dimensões de cerca de 600 por 800 mm, espessura de cerca de 8-12 mm;
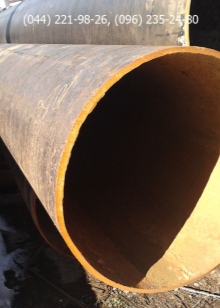
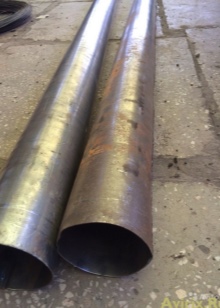
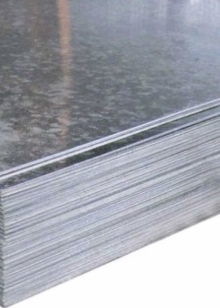
- dobradiças de metal com dobradiças;
- uma pequena parte de um cano de água roscado, diâmetro 1 / 2-3 / 4 polegadas, comprimento 50-80 mm e uma torneira de água com uma rosca dentro do mesmo diâmetro;
- peças de barras de reforço - comprimento de cerca de 500 mm, diâmetro de 12 a 18 mm, grades de ferro fundido prontas para combustíveis sólidos são adequadas;
- composição do cimento;
- tijolos;
- areia.
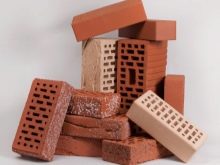
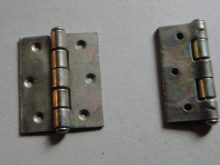
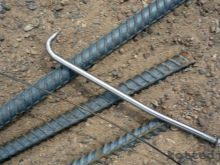
Observe que é aconselhável fazer o compartimento de combustível, a chaminé e a caldeira não em metal ferroso, mas em aço inoxidável. Embora isto esteja associado a algumas dificuldades, já que sua soldagem exigirá eletrodos do mesmo aço inoxidável ou um fio especial para soldagem.
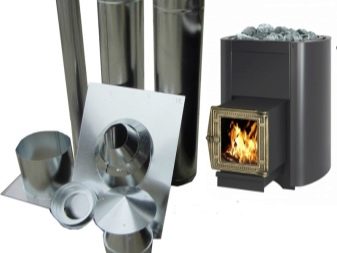
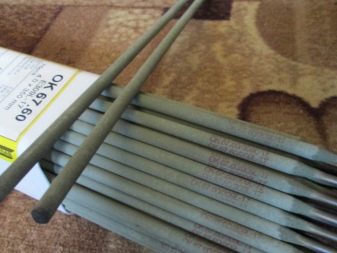
Ferramentas necessárias:
- dispositivo para soldar elementos;
- qualquer escultor de metal forte;
- eletrodos;
- guindaste de encaixe;
- metal laminado para pernas;
- cordão de amianto;
- maçanetas.
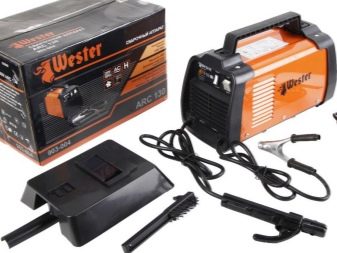
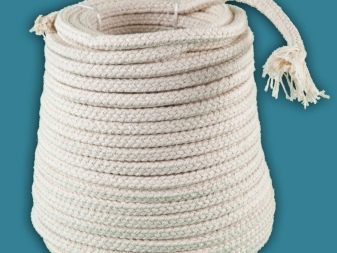
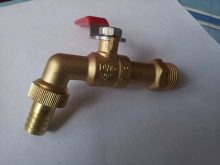
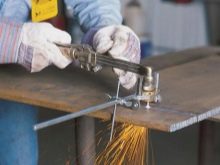
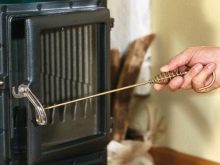
Esquemas e desenhos
Antes de começar a trabalhar, você precisa decidir qual tipo de forno - vertical ou horizontal, será o preferido. Em seguida, crie um desenho de trabalho levando em consideração todos os parâmetros - dimensões do dispositivo, configuração de seus componentes, dimensões.
Se esta é a primeira experiência de fabricação própria do fogão, é mais lógico consultar os desenhos e diagramas prontos para a fabricação de um modelo típico do dispositivo, isso ajudará a evitar erros e posterior operação incorreta da unidade . Além disso, um fogão mal montado pode representar uma ameaça à saúde e à vida humana!
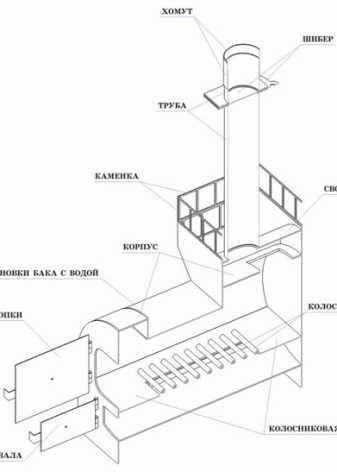
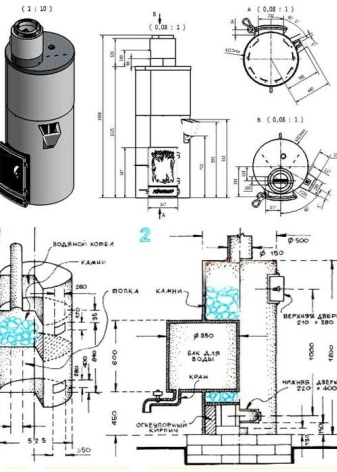
É necessário preparar a base sobre a qual o forno será instalado:
- Na área onde está prevista a instalação do dispositivo, é cavada uma fossa com dimensões de 50 x 70 x 70 cm.
- O fundo do poço é coberto com cascalho fino. Observe que a espessura da camada deve ser de pelo menos 30 cm. Em seguida, você precisa compactar esta camada o mais firmemente possível.
- Em seguida, é necessário preparar uma argamassa de cimento com base na seguinte proporção de componentes: pegar 4 a 5 partes de areia para 1 parte de cimento, diluir com água até obter uma mistura cremosa e homogênea. Despeje uma camada de entulho e deixe endurecer - esse processo geralmente leva 24 horas.
- Para criar uma impermeabilização, o material de cobertura é colocado sobre a camada de cimento endurecido em várias camadas.
- Uma camada de material de cobertura é finalmente derramada com uma composição de concreto: onde 1 parte da mistura de cimento é responsável por 2 partes de areia, 4-5 partes de cascalho e água. Depois disso, você precisa suavizar a camada resultante.
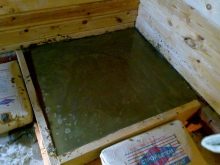
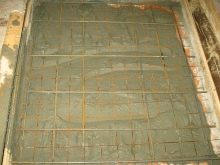
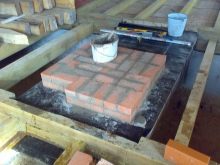
Após a secagem da fundação, uma plataforma de argila é equipada, na qual tijolos são posteriormente colocados nas mesmas dimensões - 0,7 m por 0,7 m. Como resultado, a plataforma de tijolos deve ter cerca de 15-20 cm de altura. nas paredes de superaquecimento no local, projetadas para a localização da fornalha, é colocada uma tela de proteção de tijolos, que são colocados com uma borda e presos com uma composição de argila. O melhor comprimento para esta estrutura é de 120 cm, estando o recuperador a pelo menos 20 cm dela.
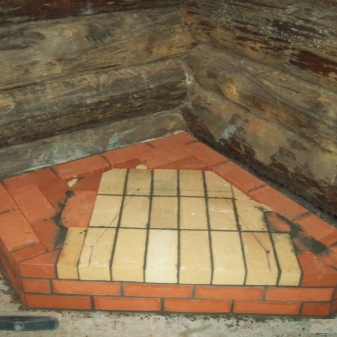
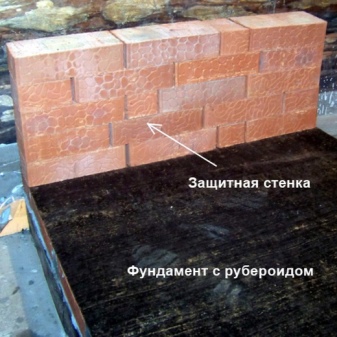
Não importa com que tipo de fogão será equipado o futuro banho - horizontal ou vertical - em qualquer caso, será equipado com aquecedor. Neste artigo, não tocaremos no tema da escolha de pedras (a maioria recomendo usar seixos de rio, balsat, quartzito, cloreto de talco ou gabbrodiabase), mesmo assim, a capacidade de calor depende do aquecedor. Não se pode simplesmente encher o fogão com pedras, pois neste caso o banho não aquecerá e todo o calor se depositará no cachimbo em forma de fuligem.
Primeiro você precisa decidir se o aquecedor estará fluindo ou aberto. No primeiro caso, as pedras serão lavadas por gases de combustão, a configuração do modo neste caso é bastante simples - basta selecionar e colocar várias pedras em várias etapas até que o efeito desejado seja alcançado. Existem nuances - neste caso, você pode vaporizar apenas quando usar lenha da mais alta qualidade e adicionar vapor apenas quando usar água. No caso de uma estufa aberta, estes requisitos não o são, mas a sua criação é mais difícil de implementar.
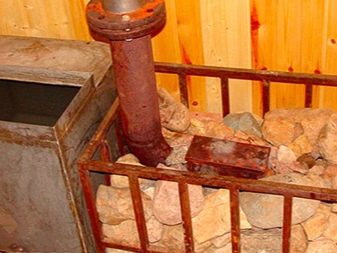
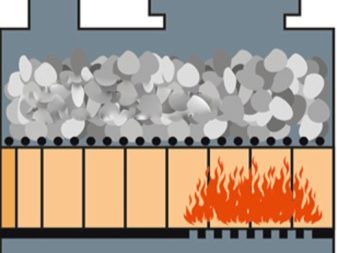
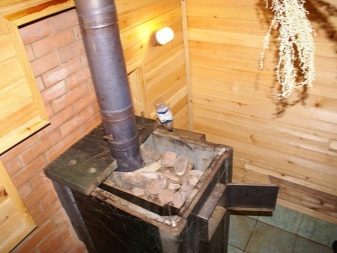
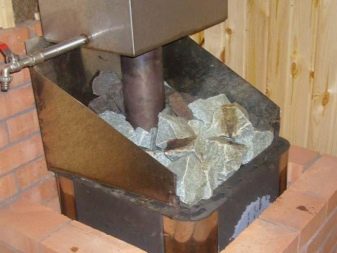
O tipo mais simples de fogão aberto é uma bandeja montada na fornalha. Esse dispositivo só é adequado para uma visão horizontal do fogão. Mas há dificuldades - cálculos preliminares, assim como o estudo de protótipos, já que a área de contato entre as pedras e as paredes do forno deve ser observada com exatidão. Um tipo diferente de aquecedor requer menos precisão, no qual o aquecimento ocorre por meio de gases de combustão, mas tal dispositivo é mais difícil de fazer.
Sem a devida experiência, é melhor dar preferência a um forno vertical - nele, o aquecedor e a cuba de água são aquecidos sequencialmente. Para pessoas mais experientes, é melhor fazer um forno paralelo, a água esquenta mais rápido neste caso. O mais difícil de fabricar é o fogão tipo campânula, no qual o fogão também fica aberto.
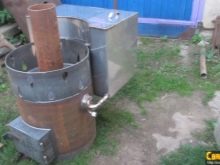
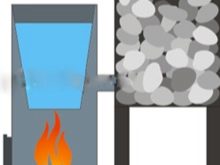
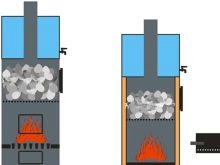
Fabricação e instalação
Não podemos esquecer que a interação com a estufa está diretamente relacionada com os riscos de possíveis queimaduras e risco de incêndio, portanto, para evitar possíveis consequências, é necessário aplicar certas regras de instalação da estufa e ter em conta as peculiaridades do seu Operação. Não será necessariamente redondo - existem outras opções. Espécies diferentes têm aproximadamente as mesmas propriedades, não é tão difícil criá-las. Apesar do forno de montagem superior em si ser leve, o trocador de calor deve ser instalado a uma altura de pelo menos 20 cm em relação ao piso. A fundação pode ser de concreto armado ou tijolo, ou pode ser montada a partir de blocos de concreto.

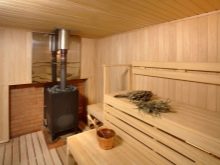
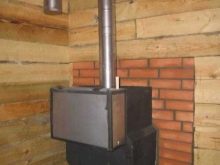
Um pré-requisito também é a presença de uma folha de metal com dimensões de 0,5 por 0,7 m na frente da fornalha e da porta do soprador. As portas certamente devem se abrir dentro do camarim ou da sauna a vapor.
A menor distância entre a chaminé, bem como outras partes metálicas aquecidas do recuperador, chaminé e lambrins de madeira das paredes e tecto é de 1 metro.
É melhor encher o tanque com água antes de acender a banheira - a umidade que entra em um recipiente de metal quente e seco está repleta de queimaduras de um choque de vapor.
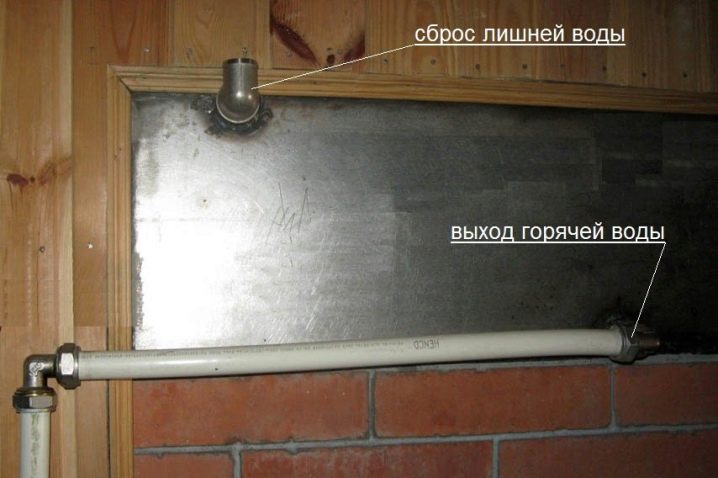
Inspecione todos os detalhes com cuidado.Antes de soldá-los, quando a instalação estiver concluída, não se esqueça de verificar suas características com uma queima de teste: eficiência, operação da bobina. Vá para a sauna, fique dentro de casa - aprecie o aquecimento do ar ao seu redor.
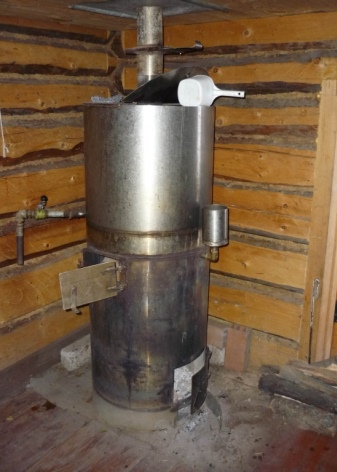
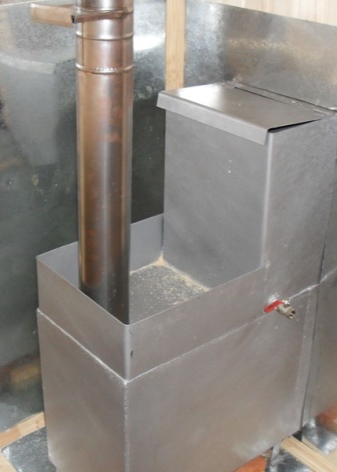
Forno horizontal
Ao fazer um forno horizontal com as próprias mãos, o procedimento será o seguinte:
- Cortar a fornalha com um moedor faz parte de um tubo com o formato exigido (em estrita conformidade com o diagrama). Como regra, este tubo terá de 0,7 a 0,9 m de comprimento.
- Fabrico de grelhas em caixilharia metálica, bem como varões de reforço paralelos ao caixilho, cuja distância entre as quais deverá ser de cerca de 50 cm.
- As grelhas são reforçadas dentro da fornalha. No caso de utilização de estruturas metálicas prontas, elas são dobradas sobre cantos metálicos, previamente soldados no interior.
- Um orifício é cortado por cima, que servirá ainda como chaminé, seu tamanho é de 15 a 20 cm. É melhor recuar 15 cm na parede posterior para que o ar quente também participe da troca de calor, e não apenas é removido o mais rápido possível.
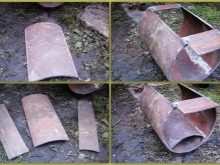
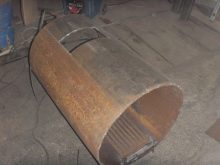
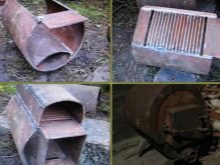
Alguns insistem em fazer um furo diretamente na parede posterior do tubo, mas não é recomendável fazer isso, pois, devido a tais manipulações, a eficiência do forno posteriormente diminui e o consumo de combustível aumenta.
O próximo passo é cortar uma folha de metal com o tamanho correspondente à parede posterior e soldá-la. Se o diagrama indica a presença de um recuperador, então a folha pertencente à parede posterior do recuperador deve ser maior para que crie um recipiente para as pedras com a sua parte superior. Uma ranhura é cortada na parede frontal, que posteriormente se tornará um cinzeiro e uma fornalha.
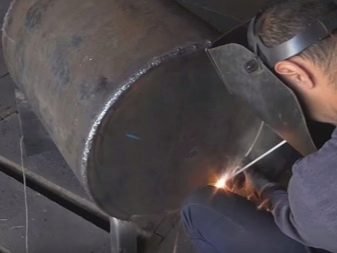
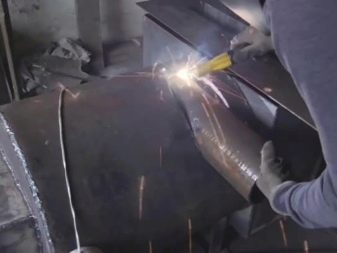
A fachada é fixada por soldagem e as portas são finalmente penduradas - geralmente são feitas de forma independente ou adquiridas em loja especializada.
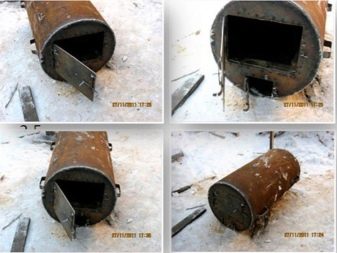
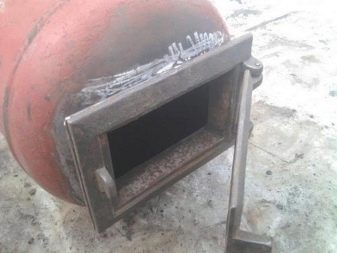
Isso é tudo - o fogão da sauna está pronto. Antes do uso, o metal deve ser tratado contra corrosão e possíveis depósitos, após todas as manipulações, as capacidades da unidade devem ser testadas conduzindo o primeiro forno de controle.
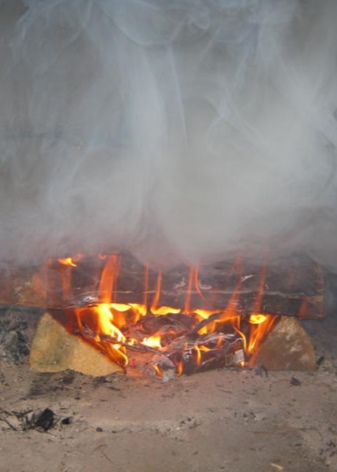
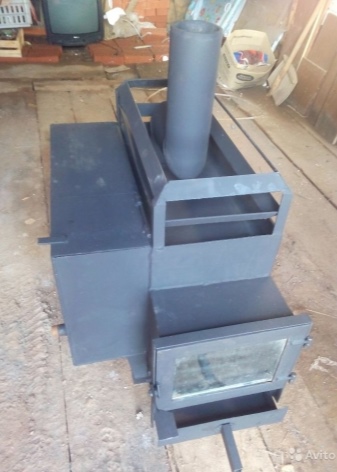
Vertical
Projetar um forno vertical é absolutamente idêntico a criar um forno horizontal, exceto por alguns pontos. Uma característica distintiva é a posição direta do tubo no espaço, quando ambas as extremidades não formam as superfícies traseira e frontal, mas a superior e a inferior, respectivamente. Em tais fornos, a seção para o arranjo das pedras está localizada diretamente na câmara do forno, como resultado, a fabricação de tal unidade será um pouco mais complicada na execução, mas o ar aquecido também será mais saturado.
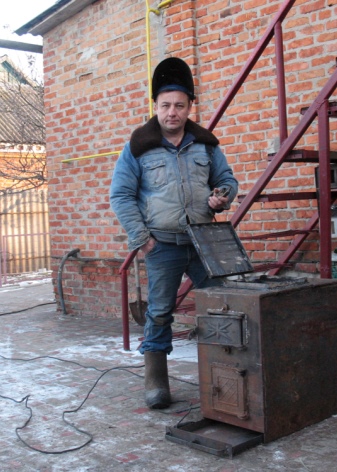
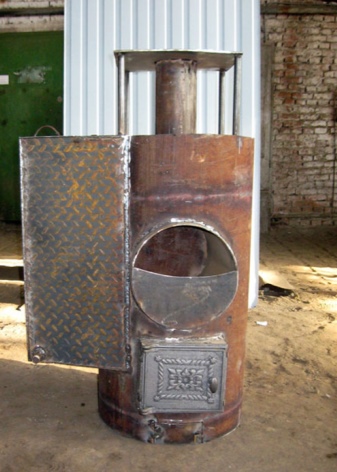
Etapas de fabricação.
- Primeiro, uma janela deve ser cortada no tubo, que servirá como uma ranhura do soprador para o suprimento de oxigênio para o combustível em combustão, e também coletará o produto de decomposição do combustível - as cinzas. Afaste-se 40 mm da borda inferior do tubo e corte uma ranhura paralelepipédica com uma trituradora ou serra, que posteriormente terá aproximadamente 80 por 240 mm de tamanho.
- No mesmo eixo, você precisa cortar outra ranhura para armazenar combustível nele - afaste-se da borda superior do orifício de sopro de 180 a 200 mm. O procedimento de corte deve ser feito com muito cuidado e o mais cuidadoso possível, uma vez que esses segmentos cortados servirão posteriormente como porta da fornalha e do soprador.
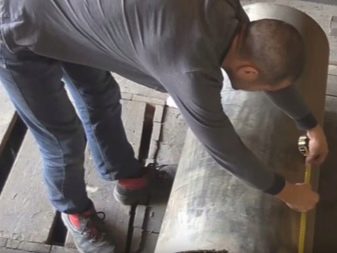
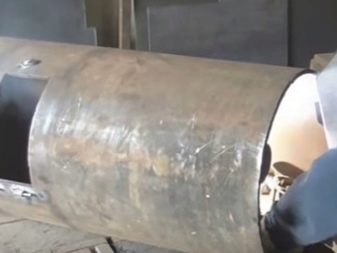
- Acima do nível da fornalha, há uma bandeja para guardar as pedras. Meça a partir da borda frontal da fornalha de 120 a 180 mm, corte uma ranhura em forma de círculo com um diâmetro de cerca de 350 mm. Observe que esta ranhura deve ser deslocada 90 graus em relação à circunferência do tubo.
- O próximo tubo é cortado com um comprimento equivalente ao diâmetro externo do tubo maior. Em seguida, você precisa cortar a parte apical em três quartos para dar ao material a forma de uma concha.
- Uma parede em branco é soldada na parte traseira com uma ranhura, na parte frontal, por sua vez, um tampão com uma porta móvel em forma de semicírculo é anexado, que será posteriormente usado como um recipiente para pedras e adicionar líquido para pedras durante o banho de vapor.
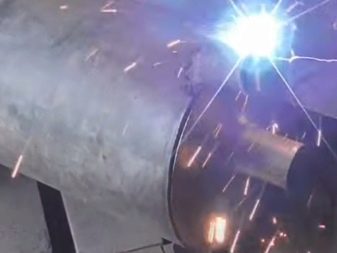
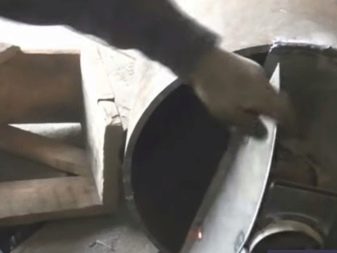
- Este corte é inserido no tubo base de forma que o recuo externo seja de 20 a 30 mm com espaço livre ao redor. Em seguida, o buraco é cuidadosamente escaldado em todo o perímetro. Se necessário, é fixado por dentro com ajuda de varões de reforço.
- Um disco circular é cortado de uma folha de metal, que é igual em diâmetro ao tubo principal em termos de diâmetro interno. Um retângulo é cortado no centro do disco - no tamanho, ele deve acomodar facilmente as grades de ferro fundido. Caso não existam, barras de reforço são soldadas na parte inferior, formando uma grade de grades.
- Na base do tanque de combustível, use uma máquina de solda para prender o tubo de base 20 cm acima do soprador.
- Recorte a base do soprador de uma folha de aço. Por baixo, o forno é colocado sobre pequenas pernas.
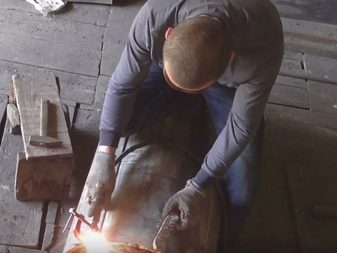
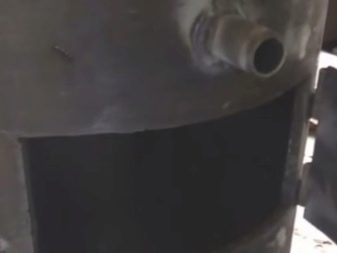
- O próximo passo é fazer uma cuba para a água, enquanto a chaminé deve passar direto por ela. O tubo principal é usado como paredes laterais, o fundo é ao mesmo tempo o arco superior da fornalha.
- O fundo é cortado de uma folha de aço de acordo com o diâmetro da parte interna do tubo, então um orifício em forma de círculo com um diâmetro de 30 a 50 mm é cortado nele, que mais tarde se tornará um chaminé.
- Uma parte da chaminé é inserida no mesmo orifício de modo que se estenda nas bordas por 100-120 mm.
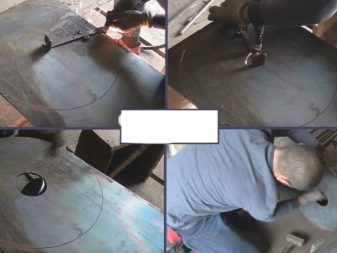
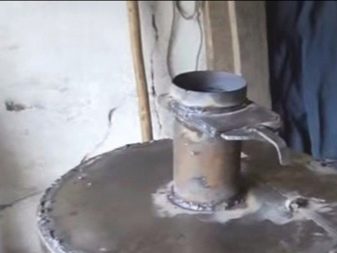
- O fundo do tanque de água é inserido na chaminé e soldado logo acima do recipiente de pedra. O cachimbo de fumaça deve estar na lateral da área em forma de concha.
- Uma cuba para água é fermentada em todo o perímetro, um orifício é feito por baixo, no qual é inserida uma torneira.
- As dobradiças são soldadas para instalar as portas no corpo. Verifique se há vazamentos enchendo o tanque com água. Em seguida, você precisa realizar o primeiro forno de teste.
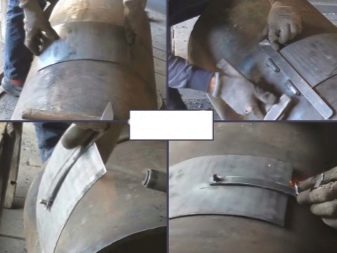
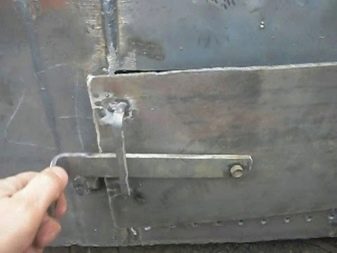
Dicas úteis
Para tornar o fogão não só funcional, mas também agradável à vista, você pode pintá-lo com tinta refratária - a tinta resistente ao calor não só lhe dará a cor desejada, mas também ajudará a proteger o metal da corrosão.
Você também pode cobri-lo com um tijolo, que não só tem uma função decorativa, mas também evita a radiação infravermelha excessiva, que é transportada pelo metal aquecido. Este tipo de raios não sobe, mas queima.
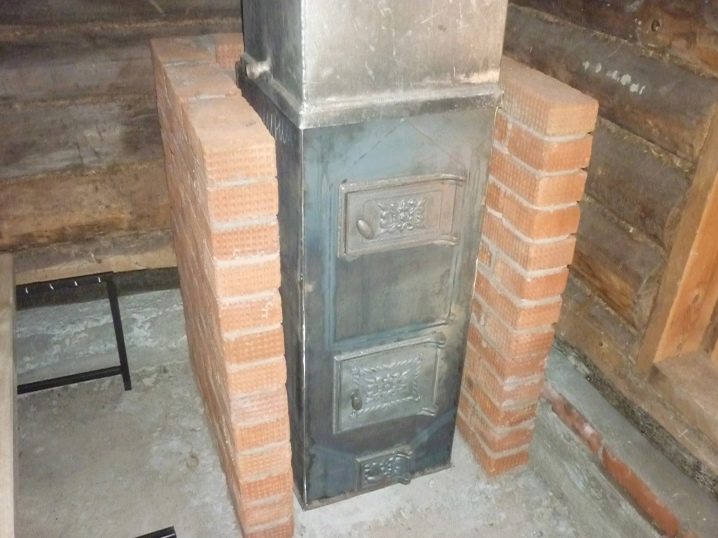
Como soldar um fogão a partir de um tubo com as próprias mãos, veja o vídeo abaixo.
O comentário foi enviado com sucesso.